Komentář: Hledání dokonalosti v dozvucích stagflace
Psala se šedesátá léta, trhy byly nenasycené, všechno rostlo. Rostly vládní výdaje, rostlo zadlužení. Koupěschopná poptávka byla nenasycena, leckde vládl trh prodávajícího. Budovaly se produkční kapacity, hrálo se o schopnost produkovat, dodávat na nenasycené trhy. Když podnikatelé, vedoucí pracovníci a manažeři na Západě řídili podniky, mohli se spolehnout na výrobu ve velkém. Objemy výroby garantovaly krytí fixních nákladů.
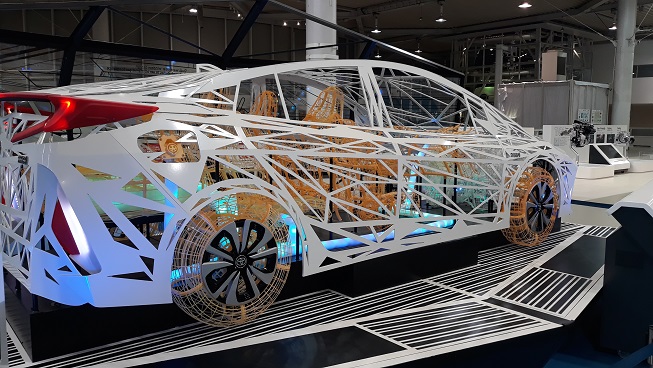
Soumrak nepružné masové výroby, který nastal v době stagflačních 70. let, měl ukázat výhody japonské filozofie. Japonec Ohno Taiichi v knize věnované pružnému systému japonské Toyoty hovoří o ropných šocích 70. let jako o mezníku. Éra vysokého růstu před ropnou krizí byla vystřídána obdobím nízkého růstu.
V pozadí problémů stálo i levné a dostupné financování, koupěschopná poptávka tažená kumulujícími se dluhy. V 70. letech ovšem recept keynesiánské makroekonomické stabilizace narazil. Ropné šoky, podobně jako stagflace, se staly předzvěstí nutnosti skutečně zvýšit úrokové sazby, zdražit financování. Ke slovu se měly dostat metody zvyšování produktivity, třeba japonské. Lékem se měl stát i reengineering, transformace organizací hledajících dokonalost.
Reengineering korporací
Organizace nákupu, výroby, prodeje a zajištění dodávek výrobků a služeb se (z)mění, zaznívalo v 90. letech. „Reengineering korporace: Manifest revoluce podnikání,“ vyslovuje název jednoho bestselleru té doby. V nové éře ovšem bude žádat dílčí úkoly opět sjednotit do ucelených podnikových procesů, vyslovili Michael Hammer a James Champy před třiceti lety.
Byla to doba, kdy se volalo po obnovení konkurenceschopnosti. Doby se změnily a měnily si i myšlenky, které ovlivňovaly podnikání. Principy se měly změnit i na poli managementu. Dost bylo fragmentace procesů, samotná dělba práce a specializace už nestačí.
Radikální transformace procesů měla být tím, co zbaví korporace neefektivních, zastaralých postupů. „Podnikový reengineering znamená začít vše znovu, začít od nuly,“ píše se v úvodu Hammerovy a Hampyho knihy. Firmy a jejich procesy je zapotřebí projektovat na míru. Změnit procesy. Pohlédnout přes a za hranice funkčních útvarů. Radikálně měnit, překopat a transformovat procesy. Dosáhnout pružné organizace schopné se rychle přizpůsobovat.
REKLAMA
Potřebu změny předznamenala už sedmdesátá léta doprovázená inflací, ropnými šoky a nečekanou stagnací. Nové nároky trhů si žádaly jiné přístupy, práce měla být organizována jinak. Byly to organizační a transformační výzvy let následujících.
V době nenasycených masových trhů a levného úvěrového financování nebyl problém prodat. Velký význam v korporacích mělo organizační uspořádání, početné štáby. Optimalizovala se oddělení, divize, nikoliv procesy. Právě tomuto už v osmdesátých letech zvonila hrana. Zvýšení úrokových sazeb a politika krocení inflace vytvořily podmínky, kdy nastoupilo utahování opasků. Způsoby řízení a vedení firem a podnikání si žádaly proměnu. V korporacích nastoupilo hledání dokonalosti, cest kudy dál.
Hledání dokonalosti
Ropné šoky 70. lety měly dopad na vlády, podnikání i společnost. Reálně nízké úrokové sazby, upřednostnění zaměstnanosti na úkor inflace. Ekonomiky se potýkaly s nulovým růstem, poválečný boom a doba nenasycené a nenasytné poptávky skončily. Vlády už dále nemohly provádět makroekonomickou stabilizaci financovanou inflačními penězi, nastoupily výzvy na poli managementu a zlepšování procesů.
Inflační 70. léta přinesla rozčarování a výzvy k hledání řešení. Jedním z amerických bestsellerů se v první polovině 80. let minulého století stala kniha Hledání dokonalosti. Thomas Peters a Robert Waterman si v této knize vydané v roce 1982 kladli otázku, jak a co dělají firmy, které jsou úspěšné.
Správnou cestou se zdál být nepočetný štáb, pružnost a úsilí malých týmů.
V Československu byla kniha Hledání dokonalosti vydána v transformačních 90. letech. V úvodu k prvnímu českému vydání akademik Leo Vodáček vyslovuje, že jen málo vyspělých zemí knihu ignorovalo. Kniha byla vydána i na naší straně železné opony, v roce 1985 v Maďarsku a o rok později v Sovětském svazu.
REKLAMA
V knize zaznívá nespokojenost s organizačními schématy, módou maticových organizačních struktur. Věže ze slonoviny analýzy, situace, kdy se nevyrábí nejlepší nebo nejspolehlivější výrobky. A pokud to takto drhne, jen zřídkakdy se vyrábí levněji, žádá si to hledat cesty k dokonalosti. Pátrat po tom, jak to dělají ti nejlepší.
Thomas Peters, Robert Waterman své šetření o hledání dokonalosti v úspěšných firmách uzavírají seznamem osmi charakteristických rysů vynikajících podniků. Jde o to aktivně jednat, být blízko zákazníkovi. Žádoucí je autonomnost a podnikavost. Čtvrtý atribut hovoří o zvyšování produktivity prostřednictvím lidí. Firmy se mají držet činností, kde vznikají hodnoty; toho, co firma umí a zná. Chce to také jednoduché organizační formy a nepočetný stav. Spojit řízení pevnou a volnou uzdou. V knize několikrát znívají slova o japonské produktivitě, inovační schopnosti a dravosti japonské konkurence.
Pohled japonských výrobců
V roce 1988 spatřila světlo světa kniha o výrobním systému japonské Toyoty z pera Ohna Taiichiho: Výrobní systém Toyoty. Nad rámec velkovýroby – „Toyota Production System. Beyond Large-Scale Production“. Vzkaz byl zřejmý, hromadnost výroby k úspěchu a konkurenceschopnosti průmyslových výrobců nestačí.
Autor knihy, Japonec Ohno Taiichi celý život věnoval zlepšování procesů. S jeho jménem je spjata filozofie JIT – potřebná věc ve správný čas na správném místě. Je-li cokoli doručeno předčasně, musí se to skladovat, inventarizovat. Představuje to nadvýrobu, může se to ukázat být nepotřebné. Klíčem k úspěchu není funkční uspořádání, ale uspořádání zajišťující tok. Když pravá ruka neví, co dělá ruka levá, hromadí se zásoby a práce vázne. Vytváří-li se cosi, pro co neexistuje zákazník, jde o plýtvání a zbytečné náklady.
Právě v japonských korporacích položili fundamenty toho, co později našlo označení jako „len management“. Dnes jde o východiska zvyšování produktivity. V předmluvě knihy o výrobním systému japonské Toyoty zaznívá, že zatímco se Západ zabýval automatizací a počítačově integrovanou výrobou (pamětníci to znají pod zkratkou CIM), japonské přístupy vše pojaly jinak. Jde například o evoluci, neustálé zlepšování („kaizen“) a odstraňováním plýtvání („muda“).
Schopnost fixní náklady snadno rozpouštět vysokými objemy výroby už není klíčem k úspěchu. Na nasycených trzích už není možné jednoduše prodat cokoli, co bylo s úsporami z rozsahu v gigantických objemech vyprodukováno.
Nastoupil trh kupujících, nehraje se pouze o schopnost vyrobit, dodat a mít nízké jednicové náklady. Trhy prodávajících zmizely, nastoupil boj o zákazníka. Ke slovu se dostala přidaná hodnota, pružná reakce a konkurenceschopná cena.
Japonský pohled, filozofie a metody
Vyrábět stejnou věc ve velkém, hromadně, jen toto k úspěchu nestačí. Doby se mění, vyrobit a distribuovat, tlačit produkci na trhy nestačí. Žádoucí je naopak japonskou Toyotou ověřený tahový systém. Zboží a vstupy jsou taženy, když jsou žádány, v množství a čase potřeby. Nikoli masové objemy výroby komponent a produktů stejného typu, ale malé objemy více typů. Pružně přizpůsobující se výroba v malých dávkách.
REKLAMA
Kanbanová karta („kanban“) doručená na jedno pracoviště se v japonských firmách stala běžným signálem potřeby dodání, doplnění zásoby. Když existuje kanban, objednávka, existuje důvod plnění zakázky. Když není kanbanová karta, objednávka a potřeba, není důvod vyrábět. Šlo by o nadvýrobu, zdroj plýtvání.
Plýtváním je třeba i pozorování chodu stroje obsluhou. Nebo také čekání na informace nebo vstupy, jako je materiál nebo specifikace. Odstraní-li se plýtvání, minimalizují se náklady. Aby se věci na pracovišti a kdekoli jinde nehledaly, nečekalo se a vše bylo připraveno k použití, vznikla metoda 5S.
První dvě „S“ si žádají věci sortovat, stanovit, kde mají být umístěné. Co je často používané, má být více po ruce. Stejně tak je nutné systematizovaně uklízet (třetí „S“), věci vracet na své místo. Čistit až se svítí. Čtvrté a páté „S“ je výzvou pro vedení – je o standardizaci a sjednocení souvisejících postupů, vedení k sebedisciplíně. Metoda 5S byla exportována do celého světa, podniky světové třídy těchto pět kroků dnes aplikuje v každodenní praxi.
Plýtváním je ale i čekání na přípravu pracoviště na novou zakázku nebo jinou práci. I taková příprava, seřízení a přestavba je výzvou pro zlepšení a zrychlení – v Japonsku k tomu vznikla metoda SMED, zkrácení a zrychlení doby přípravy pracoviště. Neproduktivní a hodnotu nepřidávající časy lze zkrátit, leccos lze mít nachystáno a dělat podle standardního provozního postupu. Existence kontrolního seznamu toho, co neopomenout, kuchařky postupu, stanovení posloupnosti, všechny tyto metody dokáží minimalizovat plýtvání.
Japonský automobilový průmysl už po druhé světové válce čelil zvláštní výzvě. Relativně nízká poptávaná množství, nutnost výroby v menších množství ve více variacích. Japonští výrobci automobilů byli po světové válce v jiné pozici než jejich západní protějšky. Museli být flexibilní, byli nuceni přestavbu těžkých lisovacích forem zkrátit z řádu hodin na dobu několika minut. Vznikla již zmíněná metoda výměna matrice v řádu minut, SMED (Single-Minute Exchange of Die).
Napříč Taiichiho knihou prostupuje uvažování o nikdy nekončícím úsilí o neustálé zlepšování. Japonci tomu říkají „kaizen“. Filozofii a přístup zlepšování po malých krocích. Taiichi proslul formulací a aplikací filozofie JIT (Just In Time). Potřebná věc má být na správném místě v ten správný čas. Následující proces má táhnout potřebné z procesů předchozích – když kompletace zakázky vyžaduje dokumentaci, tato má být „vytažena“ z procesů, které ji připravují. Vše má být synchronizováno, pracovat v taktu.
Práce nemá být protlačována, chce to uplatňovat princip táhnutí. Zásoby rozpracovaného skrývají chyby, vede to k nutnosti oprav a plýtvání. Hraje se o kvalitu, nikoli kvantitu. Práce kvapná, málo platná. Právě v Japonsku vzniklo cosi, o čemž Taiichi hovořil jako o systému managementu adaptovatelném na éru globálních trhů. Dnes to dostalo nové označení – „lean management“.